Blog post -
Brake drum or disc brakes? Eight criteria you can use to select the best brakes for your trailer
Brake drum or disc brakes? Eight criteria you can use to select the best brakes for your trailer
Generally, disc brakes are considered as the Drum brake superior technology in the commercial vehicle industry. This claim is supported by around 80 per cent of the market in Europe, which prefers disc brakes. However, there are still regional variations. Thus, England is considered a 'drum brake country', while eastern and southern Europe are increasingly turning to Trailers with disc brakes. Are drum brakes then simply an English quirk? Not at all. There are still good reasons to consider drum brakes when procuring a trailer. But so you don't just have to go with your gut when choosing, I've presented the major objective criteria for deciding in this article.
Don't forget: with the drive transformation towards more environmentally stable mobility and the introduction of the Euro 7 emission standard, the drum could become even more important due to its technical features. More about that at the end of the blog.
System expertise enable a good foundation for making a decision
As a system provider, BPW has been manufacturing trailer axles for numerous applications for 125 years and supplies trailer manufacturers with individual components, all the way down to complete running gear systems. Thanks to our comprehensive product portfolio, we have extensive system expertise for everything to do with trailers. We provide both brake discs and brake drum technology. We continuously develop both versions and put them to the acid test. They are subjected to numerous test and driving trials on the test bench and the road. We aim to draw on our experience to provide the best possible choice of suitable brakes for individual needs:
The self-contained design protects drum brakes in off-road use
Drum brakes show their strengths wherever a robust system is an advantage. The fact that the brake is concealed in a closed drum protects it against mud, dust and other dirt. So it makes sense to equip vehicles with drum brakes which are predominantly driven off-road, such as tippers, trailers and low load trailers.
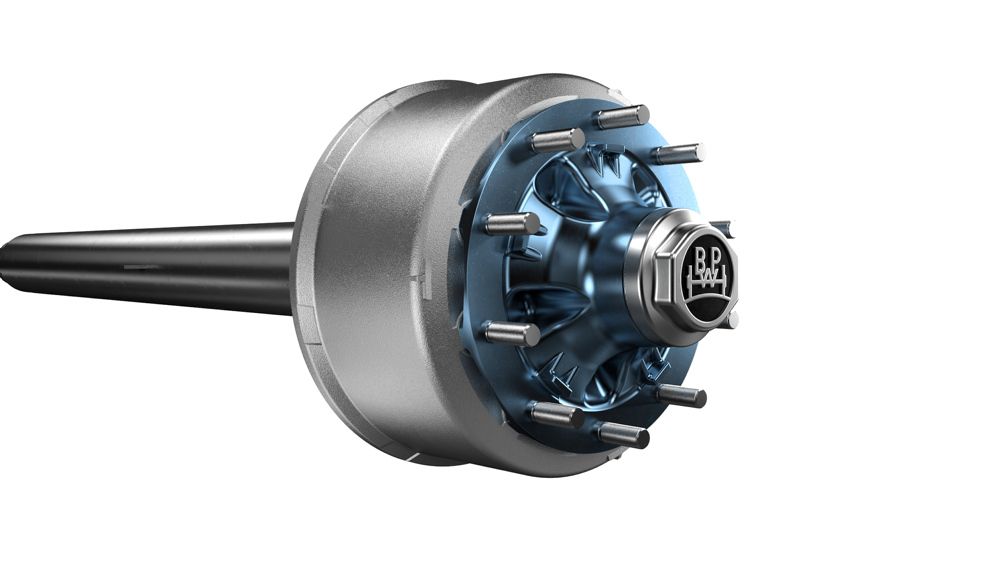
Caption: BPW brake ECO Drum
Drum brakes are more resilient in seasonal use
This applies all the more if the trailer is only used at certain times and left standing off-season. The brake linings of disc breaks are at risk of vitrifying if they are not used enough or there is a lot of down time; plus brake discs can corrode over time, as then are constantly exposed to the wind and weather. This is not only the case for construction vehicles, but also with trailers which are used in the agricultural and forestry transport environment. Or for semi-trailers which are used in multi-mode traffic and travel long distances on rails or water and only short routes on their own axles.
Drum brakes are forgiving of errors and moderate maintenance
A drum brake is basically a robust component. It often proves itself resilient even with only moderate maintenance. Plus, if a semi-trailer is used with alternating tractor units or those which also have a drum brake, this proves itself to be the better variant. Disc brakes, on the other hand, require good tractor/trailer synchronisation to prevent the trailer from over-braking with a drawbar trailer. This would lead to uneven wear on the brake linings and, as a result, the friction combination would not achieve its theoretical maximum life-span.
Disc brakes are the first choice for on-road use
On the other hand, tarmac roads are the natural environment for trailers with disc brakes. Following its establishment for on-road use in trucks, today, the technology is also standard in trailers. If the coordination with the tractor unit is good, then truck drivers often report better braking performance. The reason for this is also the disc brake design principle, which is less susceptible to over-heating when the braking effect is very heavily utilised. There is no 'fading' here, which is sometimes the case with drum brakes. In combination with the other advantages, international long-distance and inner-city traffic is generally the domain of disc brakes.
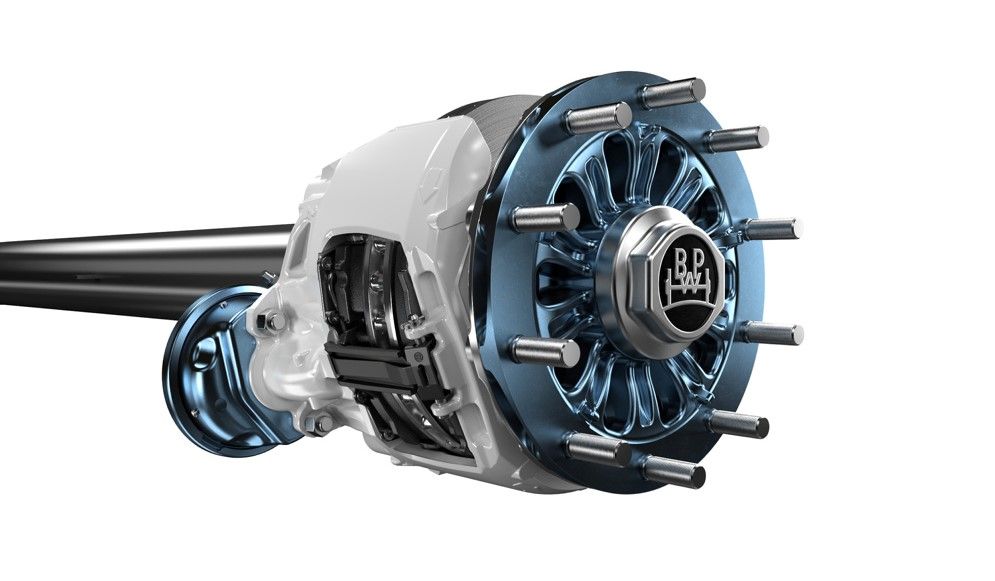
Caption: BPW brake ECO Disc
Disc brakes enable a clear payload benefit
Disc brakes have a weight advantage. At BPW, the ECO Disc (TS2 4309, offset 120) in a three axle suspension has a weight advantage of thirty kilogrammes compared to the drum brake. With the ECO Disc TS2 3709 with offset 0, there is even up to ninety kilogrammes more useable load. This makes disc brakes perfect for transport in which every kilogramme of usable load counts, such as for tank silos, as well as coil, paper and beverage transport.
A question of the price and operating costs
Last but not least, the decision for or against disc brakes depends on the price. This is also the factor which is most difficult to evaluate, as it depends on many fleet-specific conditions. Disc brakes and drum brakes are not necessarily worlds apart in terms of price. But whether that is actually the case in reality depends largely on the price policy of the respective vehicle manufacturer. The same applies for the price of wear and spare parts. The individual price policy of the OE manufacturer or provider of the independent aftermarket also plays a role here. Fleets with their own service operation benefit from a high level of transparency here, while others are dependent on information from the garage.
The maintenance required for disc brakes is generally lower
The maintenance required for disc brakes is often lower, as the relevant wear parts are easily accessible thanks to the open construction and therefore replacing them takes less time, at least in theory.
At BPW, we have taken easy service and repair for braking technology to the next level: thanks to our patented ECO principle, i.e. fast disassembly and assembly according to the formula 1 method via a central axle nut, the variants score points with the time-saving exchange of discs, drums and linings. With the ECO Disc in a three axle, this can even save up to three hours and therefore reduces garage costs compared to standard competitors solutions. However, there is a systematic disadvantage in maintenance effort with drum brakes due to the regular lubrication of bearings in brake camshafts and automatic slack adjusters.
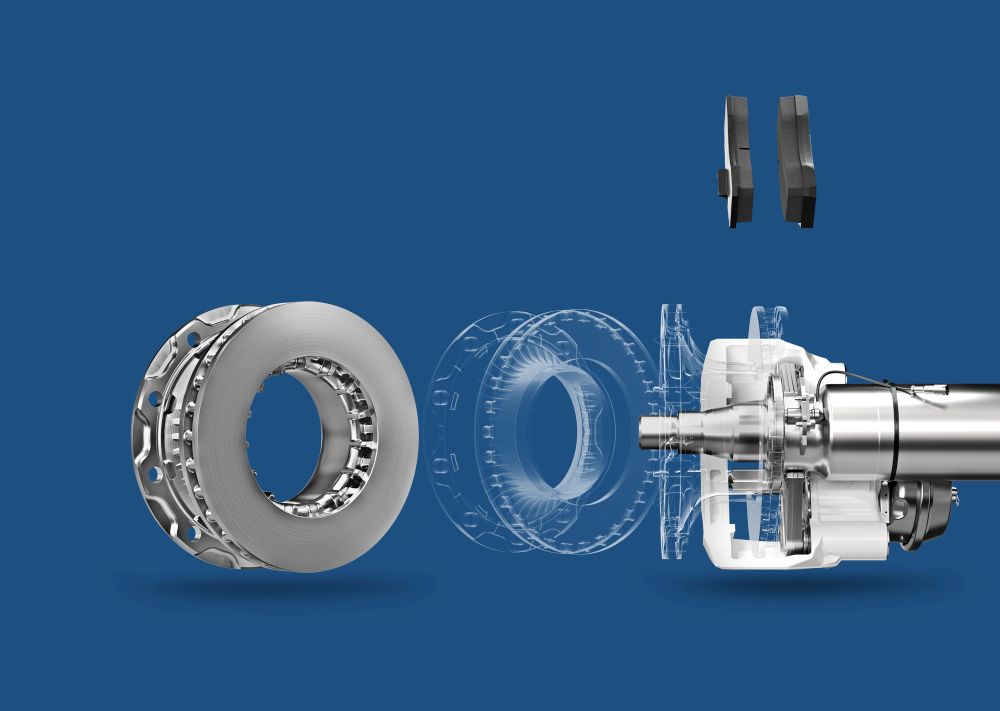
Caption: Rapid wheelend disassembly like in Formula 1 for BPW ECO Disc and ECO Drum with ECO Technology
Drum brakes require regular maintenance, but on the other hand, the wear parts, such as the brake linings and drum, last longer than brake pads and brake discs. The decision for or against a brake system is highly individual in this point in particular and depends on several factors, such as the idle times of the wear parts, spare part prices, the holding period of the vehicle and whether you have your own garage, for example, or if you rely on third party garages.
Higher demand for disc brakes create higher residual values
Ultimately, disc brakes are favoured in terms of the trailer's residual value. After working as a trailer with this type of equipment, the demand in the aftermarket is higher. That's why better prices can generally be achieved for the used trailer. However, with increasing performance, these positions become relative.
Lower particle emission with drum brakes
During servicing, the encapsulated construction of drum brakes is usually more of a disadvantage. But this may soon turn into an advantage. With the introduction of the emissions standard Euro VII from July 2027, the legislator will initially also regulate particle emissions - among other things through abrasion on brake linings. Wear is lower with drum brakes today, this also means fewer particle emissions are created and it is anticipated that it will be much easier to capture the unwanted dust particles, so they never make it into the air in the first place. There will also be suitable solutions for disc brakes, although that may require more effort.
The advantages of drum brakes for e-mobility
Car manufacturers are already equipping their e-vehicles with a drum brake on the rear axle. The axle is braked by the kinetic energy recovery through recuperation, i.e. through an electric brake resistance and the kinetic energy can be restored as electric energy in the drive battery. The brake on the rear axles of e-vehicles has much less to do than in a standard vehicle. In E-trucks, the same effect could result as in vehicles used in seasonal or combined traffic: in the worst case, the disc threatens to corrode and the result could be uneven braking which will be seen as a fault be technical services during regular checks.
Always be on the safe side with BPW braking systems
As you can see: the selection of suitable brakes depends on many factors. Both technologies have their benefits, but they predominantly reveal their advantages if they are attuned to the specific usages of the trailers. Still, one thing is certain: fleet operators who rely on BPW brake systems will have a economically efficient solution with optimised operating costs. BPWs system expertise gained over 125 years of experience ensures that all brakes are technically developed to a high standard and can safely perform their service - regardless of whether a drum or brake is used.